In a fast-paced and highly competitive industrial landscape, manufacturers face increasing pressure to improve efficiency, reduce costs, and adapt to a changing workforce. As labor shortages and operational costs continue to rise, automation has shifted from being a competitive advantage to a critical necessity. One area where automation is proving to be a game-changer is palletizing. Automated palletizing solutions are not just about increasing throughput; they address a wide array of challenges that modern businesses face.
The challenges driving automation
1. Labor shortages
Labor shortages have become a significant challenge for manufacturers globally, driven by an aging workforce and declining interest in manual, repetitive jobs among younger generations. This labor gap has put immense strain on production processes, particularly in tasks like palletizing, which require repetitive physical effort.
Automated palletizing systems eliminate the need for constant human labor in these roles, allowing businesses to maintain productivity levels even amid workforce shortages. By reallocating human workers to more value-added tasks, companies can also improve job satisfaction and employee retention.
2. Rising labor costs
Labor costs have been steadily increasing due to inflation and the competitive labor market. In roles that are physically demanding and repetitive, manufacturers often struggle to retain workers, leading to high turnover rates and significant recruitment and training costs. Automation offers a sustainable solution by reducing reliance on manual labor, cutting down on overtime expenses, and minimizing the costs associated with high employee turnover.
3. Health and safety concerns
Palletizing is physically taxing, involving heavy lifting, repetitive movements, and awkward postures that increase the risk of workplace injuries. Such injuries not only impact workers but also result in lost productivity, higher insurance premiums, and compliance risks. Automated palletizing systems drastically reduce these risks by taking over the most physically demanding tasks, ensuring a safer and healthier workplace.
4. Demand for operational efficiency
Manual palletizing processes are prone to errors, inconsistencies, and slow throughput, all of which can hinder overall productivity. Automation ensures consistent performance, precise stacking, and faster cycle times, enabling businesses to meet customer demands without compromise.
The strategic benefits of automated palletizing
1. Increased productivity
Automated palletizing systems can operate 24/7, delivering unparalleled productivity compared to manual processes. These systems ensure faster stacking speeds and consistent output quality, allowing manufacturers to handle increased production volumes without additional labor.
2. Improved accuracy and consistency
Automation eliminates human error, ensuring that products are stacked uniformly and securely every time. This consistency reduces the likelihood of damaged goods during transit and improves overall supply chain reliability.
3. Scalability
Automated palletizing systems are inherently scalable, allowing manufacturers to adapt to changing production demands. Modular and flexible designs mean businesses can expand or reconfigure their systems as needed, ensuring long-term adaptability.
4. Cost savings
While automation involves upfront investment, the long-term cost savings are substantial. Automated systems reduce labor costs, minimize waste due to errors, and lower expenses related to workplace injuries and insurance premiums. Additionally, the ROI for automated palletizing systems is often realized within a few years, making it a financially sound decision.
5. Enhanced workplace morale
By automating repetitive and physically demanding tasks, companies can create a more positive work environment. Employees can focus on higher-value activities, such as equipment monitoring, quality control, or process optimization, leading to greater job satisfaction and reduced turnover.
Addressing common concerns
Adopting automation comes with questions and concerns, but many perceived barriers—like cost, technical complexity, and implementation disruptions—are easier to overcome than you might think. Here’s how manufacturers are tackling these challenges and making automation work for them.
1. Initial investment
One of the most common barriers to adopting automation is the perceived high upfront cost. However, many manufacturers find that the ROI from automation—through increased productivity, reduced labor expenses, and fewer errors—quickly offsets the initial expenditure. Moreover, financing options and incremental automation strategies can help businesses manage these costs effectively. To calculate the ROI of a Robotiq palletizing solution on your factory floor, download our ROI calculator!
2. Technical skills gap
Some manufacturers worry about the technical expertise required to implement and maintain automated systems. Modern palletizing solutions are increasingly user-friendly, with intuitive interfaces and minimal maintenance requirements. Additionally, automation providers often offer training and ongoing support to bridge any skill gaps.
3. Disruption during implementation
Introducing automation may initially disrupt workflows, but careful planning and phased implementation can minimize downtime. By partnering with experienced automation providers, manufacturers can ensure a smooth transition with minimal impact on operations.
Real-world success stories
Many manufacturers have already reaped the benefits of automated palletizing. For instance, companies in industries such as food and beverage, consumer goods, and logistics have reported significant gains in efficiency, cost savings, and worker satisfaction after adopting automation. These success stories highlight how automated palletizing systems can address industry-wide challenges while providing a solid foundation for future growth.
Conclusion
As manufacturers navigate the challenges of labor shortages, rising costs, and the need for greater efficiency, automated palletizing emerges as a strategic imperative. By addressing critical pain points and delivering measurable benefits, automation is no longer a luxury but a necessity for businesses looking to remain competitive in a rapidly evolving market.
Now is the time to evaluate your palletizing processes and consider how automation can transform your operations. With the right approach and solutions, you can future-proof your business, achieve sustainable growth, and create a safer, more efficient workplace for your employees. Take a deep dive with our Automated Palletizing Buyer’s Guide or contact one of our experts for advice on where to start with automation!
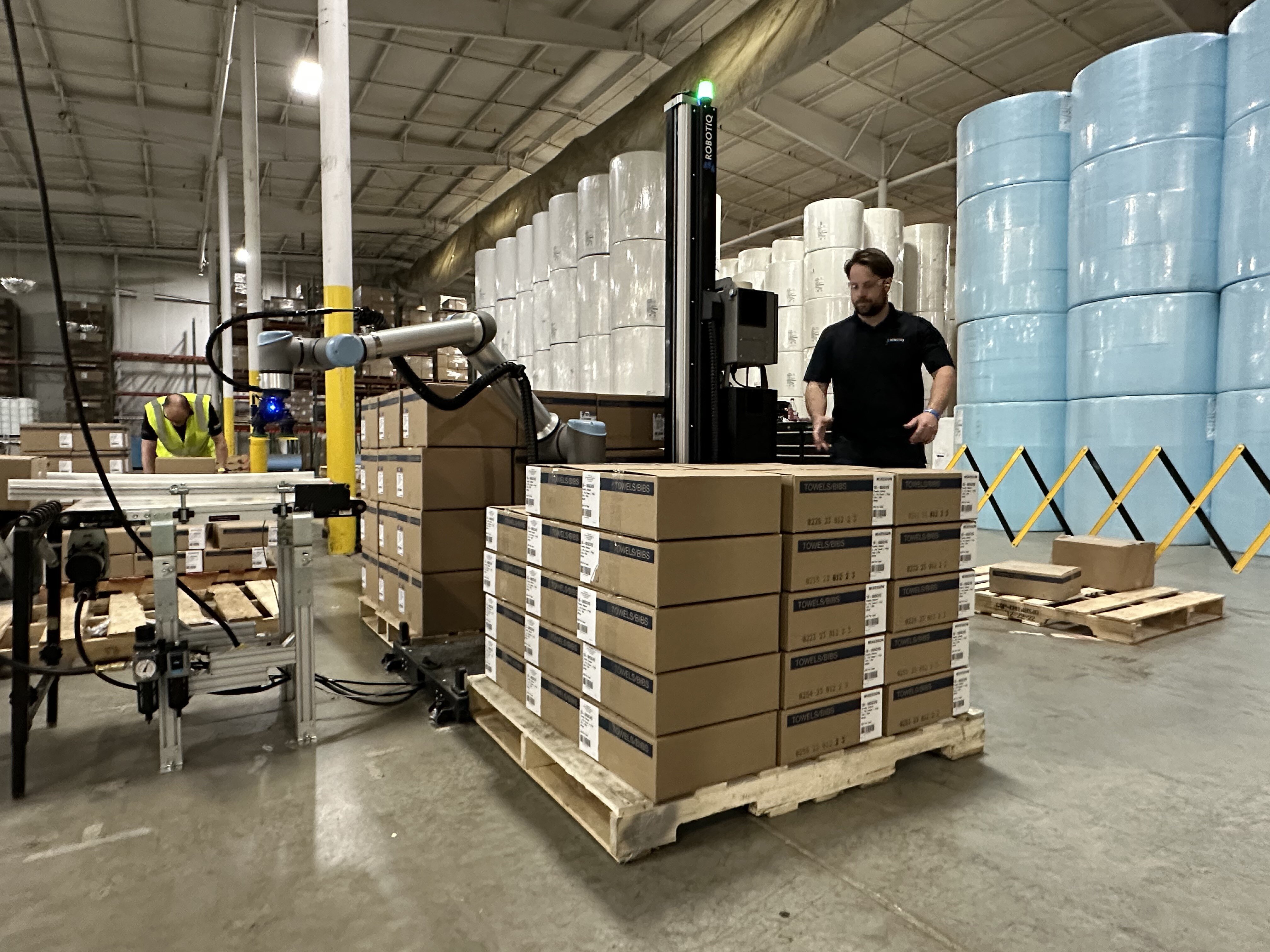
The post “Why automating palletizing is a strategic imperative” by [email protected] (Samuel Bouchard) was published on 03/18/2025 by blog.robotiq.com