Palletizing may seem simple—until you’re lifting 43-pound boxes all day, stacking them six feet high, and struggling to find workers willing to take on the grueling task. For one pizza dough manufacturer, this bottleneck wasn’t just slowing production—it was making staffing a constant headache. The solution? Automation. See how Robotiq’s PE20 palletizer helped them overcome space constraints, reduce reliance on temp labor, and keep production moving.
The company
This particular customer has a singular focus: they make and distribute pizza dough. With just a handful of SKUs, their process is streamlined—but not without its challenges. Their dough balls are packed into boxes and shipped to distributors serving restaurants, retail, and food service businesses.
The challenge: a job no one wanted
Palletizing might appear simple, but for this manufacturer, it became a major bottleneck. The boxes weighed up to 43 pounds each (20 kg), and stacks reached up to six feet high (1.8m). The repetitive lifting and overhead work made it an incredibly strenuous job—one that was almost impossible to staff.
The company relied heavily on temp labor to fill their two 10-hour shifts, which came at a high cost and with constant turnover. In some cases, production had to slow down just to shift workers to cover the palletizing task. It was clear: this job needed automation.
Why Robotiq’s solution was the perfect fit (literally)
Several factors made Robotiq’s palletizing solution the right choice:
- Handling Heavy Boxes – The company was initially considering a heavier-duty industrial robot, but the timing was perfect: Universal Robots had just increased the payload capacity of the UR20 from 20 kg to 25 kg. This meant that instead of going with a larger system, they could deploy the compact and efficient PE20 cobot palletizer, which was more cost-effective and better suited for their needs.
- A Compact Footprint – Space was tight. Traditional industrial palletizers were far from ideal due to their large footprint. Robotiq’s solution, with its flexible and compact design, was able to fit into the customer’s available space with just inches to spare. With the help of Robotiq’s application team, the setup was optimized to function seamlessly within these constraints.
- Smart Path Planning – In a cluttered environment, movement matters. Robotiq’s software allows users to define restricted zones, ensuring the robot can operate efficiently even in close quarters. This was critical in making the system work within the customer’s workspace.
Advice for manufacturers considering automation
If you think automation isn’t possible for your facility, think again. This customer originally assumed their constraints—box weight, limited space, and the nature of their operation—would make robotic palletizing impossible. But by bringing the challenge to Robotiq, they found a solution tailored to their needs.
For any manufacturer facing labor shortages, high turnover, or physically demanding tasks, the key takeaway is this: don’t rule out automation before exploring the possibilities. With the right technology and the right team, even the toughest challenges can be solved.
If you’re struggling with a similar bottleneck, reach out. We’ll help you find a way to make automation work for you.
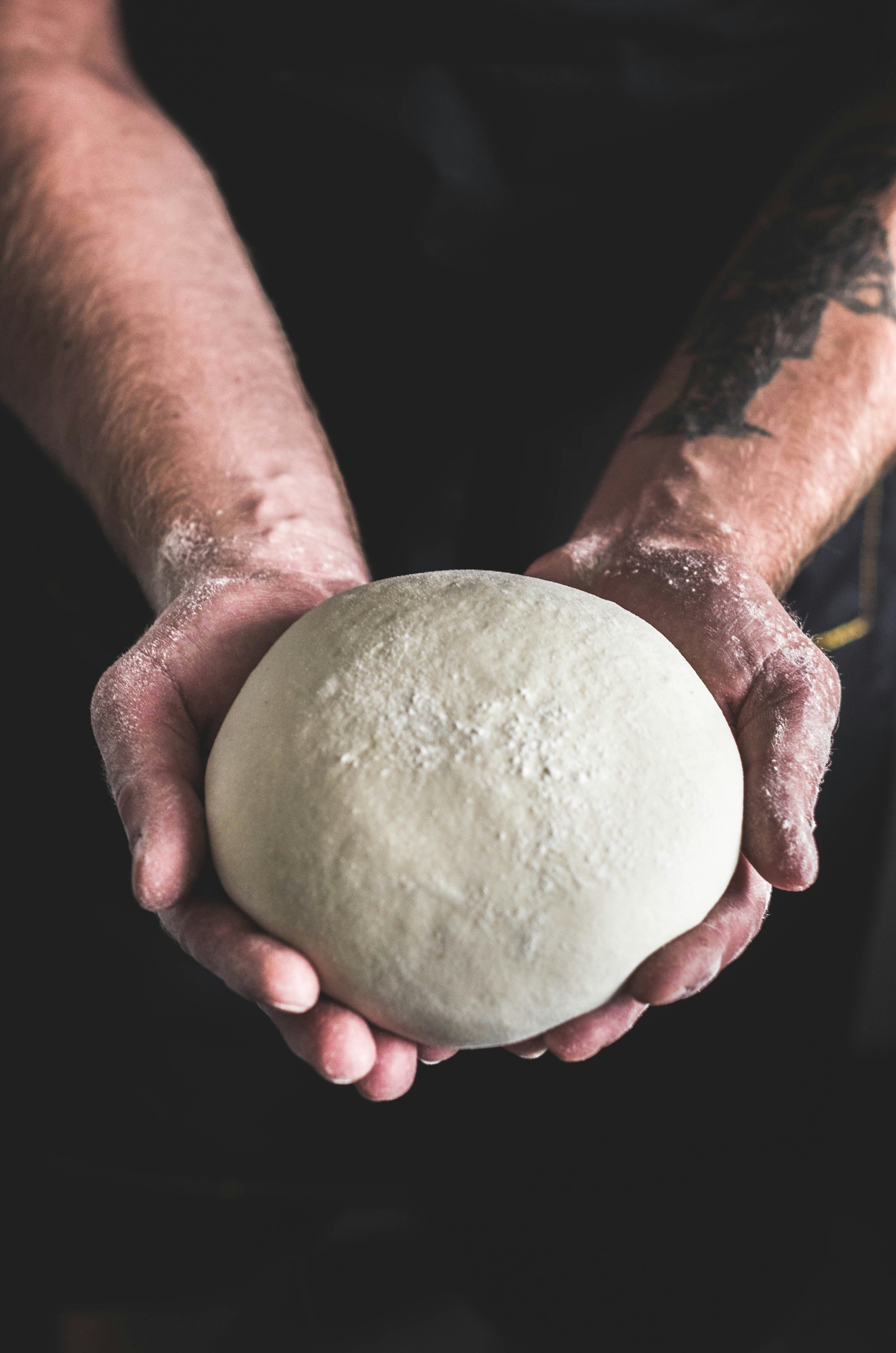
The post “Automation that delivers: how a pizza dough manufacturer tackled palletizing challenges” by Gaelen Harsch was published on 03/20/2025 by blog.robotiq.com