When a manufacturer considers implementing automation in their operations, one of the first questions that typically arises is: What is the cost of a cobot? At first glance, this seems like a straightforward inquiry, but the answer is far from simple. Adding a cobot to your production line isn’t just an expense—it’s a strategic investment in efficiency, consistency, and long-term savings.
The price varies based on the model and features, but with the right grippers, software, and setup, a cobot can transform your operations. Understanding the full cost picture helps you make an informed decision and unlocks the true value of automation. Let’s break it down so you can see how quickly a cobot can pay for itself.
As with many products, the cost of cobots varies widely. This variability can be compared to something such as the price of a car. Just as a basic economy car can be purchased for a few thousand dollars, while high-end luxury models can cost tens of thousands, cobots also come in various price points.
Generally speaking, the cost of a cobot arm can range from as low as $15,000 for an entry-level Chinese-made model to upwards of $60,000 for top-of-the-line, high-quality models that boast superior reliability and advanced features.
However, a cobot arm by itself doesn’t do much. Just as a car needs fuel, maintenance, and a driver to operate, a cobot needs additional components to function in an industrial setting. This leads to a crucial second consideration: the cost of the entire cobot system, not just the arm itself.
Cobot System Costs: What’s Included?
When you’re budgeting for automation, it’s important to recognize that the cobot arm is only one part of the equation. To truly get value from the cobot, you’ll need additional elements, including:
- End-Effector: This is the part of the system that interacts with the product, such as a gripper or suction cup, and its cost varies depending on the specific task.
- Integration & Setup: Depending on your production line, you may need to modify existing systems (conveyors, air systems, electrical infrastructure) to accommodate the cobot.
- Software & Programming: A cobot might require custom programming to function in your specific environment, or, in some cases, you may need a specialized interface to help the cobot interact with your existing systems.
If you’re opting for a turnkey system where everything is pre-packaged and ready to go, the cost of a cobot system can be quite reasonable.
However, if your application requires a more customized solution, the cost can escalate quickly. In these cases, the cost of engineering expertise and the time required to create a tailored system can drive the total cost much higher.
Custom Solutions Considerations
One of the biggest factors that can increase the cost of a cobot system is custom engineering. If you have a complex task that requires specific tooling or specialized modifications to your production line, you’ll need to invest in engineers to design and implement the solution.
Engineering talent, particularly those experienced with automation systems, is in high demand and can come at a premium. Custom solutions also tend to have longer lead times, meaning you’ll need to plan ahead for the potential delays in getting your system up and running. Additionally, custom systems might face reliability challenges since they often incorporate unique components that have not been mass-produced or thoroughly tested over time.
That being said, a custom solution may be necessary for certain tasks, and in those cases, the increased investment could yield valuable improvements in efficiency and productivity.
However, if your task is relatively simple, there are many off-the-shelf systems that can do the job effectively, keeping costs down.
What is the Real Cost of Automation?
When considering the cost of a cobot system, it’s essential to focus on the total cost of automation, which includes both the initial investment and ongoing operational expenses. This is where the concept of Return on Investment (ROI) comes into play. ROI is the key metric that manufacturers need to consider to assess whether the automation project is worth the investment.
To calculate ROI, you need to document the current cost of operating your production line or the specific task you plan to automate. This includes the labor costs associated with running the line, such as the number of employees needed, their hourly wages, and any other costs related to the operation. You should also factor in the annual output of the line, both in terms of revenue and gross profit. This will provide a baseline for comparing the costs before and after automation.
Once you have the baseline, you can calculate the cost of automation. This includes the cost of the cobot system itself, as well as any collateral expenses such as line modifications, downtime, and additional infrastructure costs. You can use our Lean Robotics ROI calculator as a tool to estimate the ROI of a cobot on your factory floor.
The Payback Period
Typically, companies look at the payback period over a five-year horizon. The payback period is the time it will take for the savings generated by the cobot system to equal the initial investment.
For example, some manufacturers have seen extreme ROI cases, such as a vaccine manufacturer who recovered a $200,000 investment in just two months. While this is an exceptional case, it illustrates the potential for rapid returns when the system enables significant increases in production output or when gross margins are high.
The Cost of Inaction
While calculating ROI is important, manufacturers also need to consider the cost of inaction. If you decide not to invest in cobot automation, you may continue facing increasing labor costs, rising production costs, and potential challenges with meeting customer demand. The cost of not automating can eat into your margins over time as labor becomes more expensive, and you’re less productive than your competitors who have adopted automation.
In many industries, the pressure to reduce costs and increase output is only growing. As labor shortages and economic challenges persist, the decision to automate becomes more urgent. By investing in cobots now, you’re securing your future competitiveness in an increasingly automated world.
The Hidden Benefits of Cobot Automation
Beyond the obvious financial benefits, cobots also offer intangible advantages that can have a significant impact on your business. These include:
- Reduced Ergonomic Risks: Cobot systems can take on repetitive, physically demanding tasks, reducing the risk of injury for your workers and improving workplace safety.
- Employee Morale & Retention: By automating repetitive tasks, you allow your employees to focus on higher-value work, which can improve job satisfaction and morale.
- Flexibility and Scalability: Cobot systems are highly flexible and can easily be reprogrammed for new tasks or scaled to meet increased demand. This makes them ideal for businesses that need to adapt quickly to changing market conditions.
- Enhanced Customer Perception: Many businesses find that customers appreciate seeing automation in action, which signals innovation and a forward-thinking approach.
Ready to invest in a cobot?
Speaking with an expert can provide valuable insights to ensure you make the right decisions for your automation needs. Our experts can help you assess your goals, understand the technical capabilities of cobots, and guide you through the process of selecting and integrating the best solution for your operations.
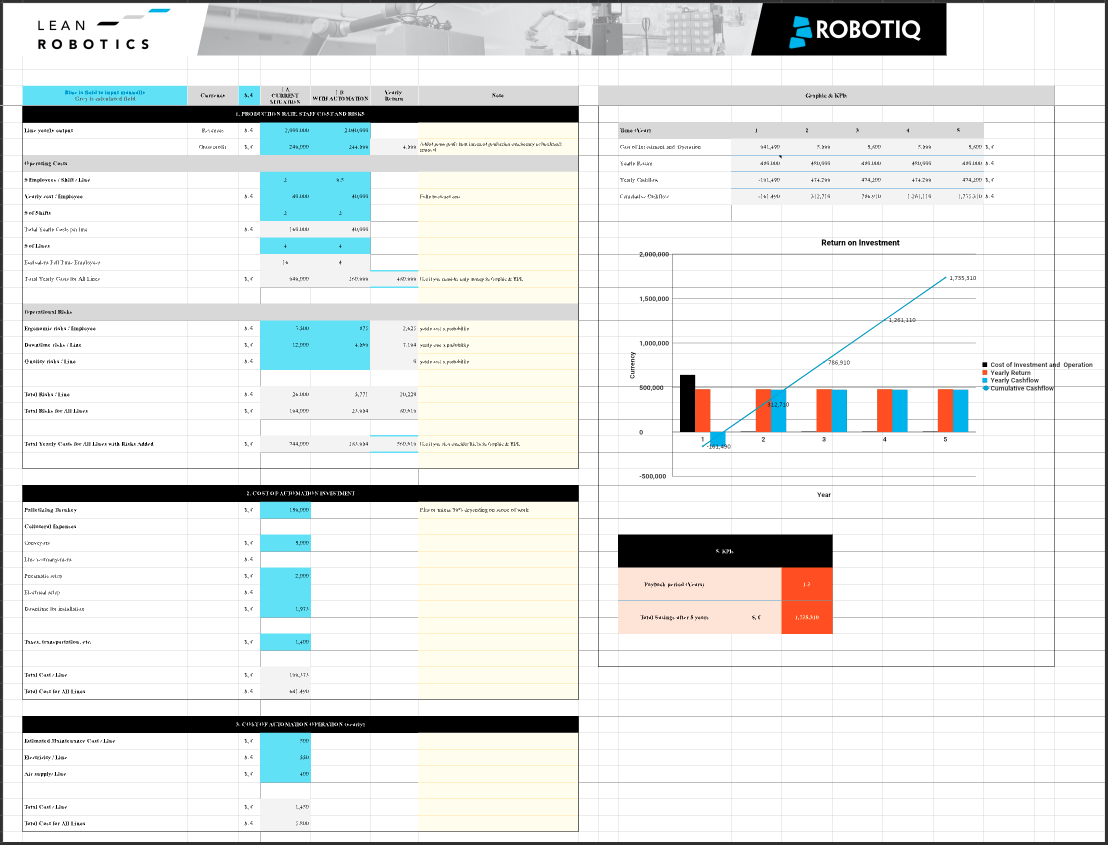
The post “How Much Does a Cobot Cost? Understanding ROI and the Bigger Picture” by [email protected] (Samuel Bouchard) was published on 02/25/2025 by blog.robotiq.com