After years of hesitation, a well-known chocolate manufacturer in Quebec, Canada finally took the leap and modernized their automated palletizing process. What changed? The right timing, the right problem, and the right solution. Their journey highlights key takeaways for food manufacturers considering upgrading their automation but unsure when or how to start.
The Challenge: A Bottleneck in Production
This company, with multiple locations and over a thousand employees, had been expanding its retail offerings. More products meant more demand—but also more strain on production.
Their biggest issue? The second shift. Like many manufacturers, they struggled to find and retain workers, especially for late-hour positions. On top of that, their existing industrial palletizer was unreliable, prone to breakdowns, and eventually failed completely last summer. This left them with a clear choice: either stick with an outdated, labor-intensive process or invest in new automation to keep up with demand.
The Turning Point: An Engineer Who Saw the Big Picture
Automation wasn’t a new idea for them. The engineering manager had been in discussions with Robotiq about palletizing solutions for a few years while working for a different company, but never had the right opportunity. When he joined this chocolate maker, he immediately recognized that upgrading to a modern, robotic palletizer could solve their labor issues and improve efficiency.
With an ROI in under 2 years and the flexibility to expand, the decision became an easy one.
Key Benefits Achieved
- Space Optimization: Floor space was tight, but the new palletizer’s advanced software allowed them to install it close to existing structures without interfering with operations.
- Fast Installation: Within one day, they were running their first SKU. Within two days, full integration was complete.
- Ease of Use: The previous system required a single expert to troubleshoot and maintain it. Now, even second-shift maintenance staff could operate the equipment with confidence.
- Scalability: With their first robotic palletizer up and running, they’re already planning for a second one.
What Other Food Manufacturers Can Learn
- Don’t Wait for a Breakdown to Automate. If your equipment is unreliable, don’t risk productivity losses. The earlier you upgrade automation, the sooner you start seeing returns.
- Think Beyond Labor Shortages. Automation doesn’t just solve hiring challenges—it can optimize space, speed up production, and increase flexibility.
- Consider Ease of Use. Modern solutions are designed for simple operation. Your team doesn’t need to be experts in robotics to run and maintain them.
- ROI Can Be Faster Than You Think. A payback period under 2 years is reasonable, but in many cases, benefits start appearing immediately with increased productivity and team morale.
This chocolate maker is proof that automation doesn’t have to be complicated or disruptive. When the right conditions align, the transition can be smooth—and the results, game-changing.
If you’re facing similar challenges, now might be the right time to take that next step.
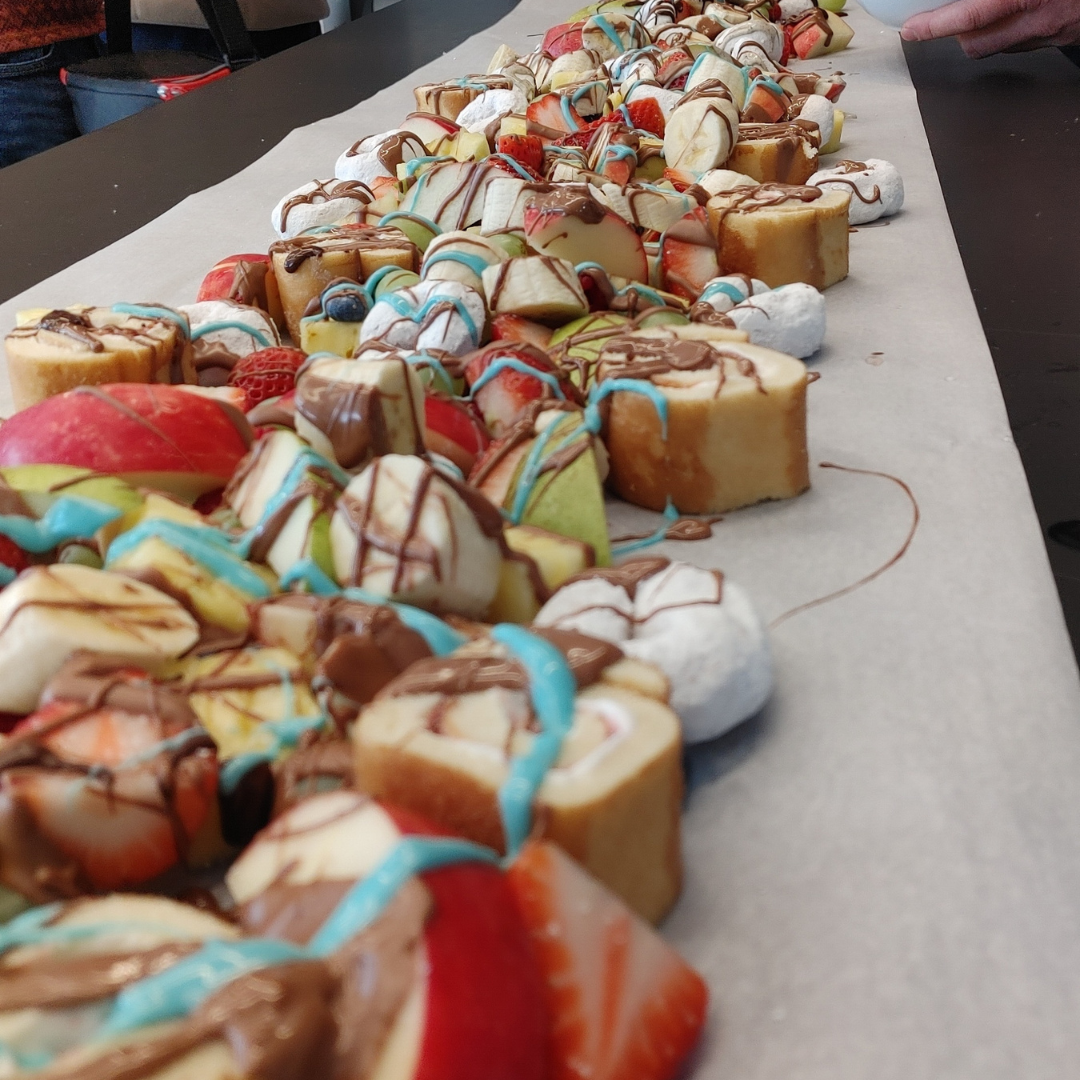
The post “Why a Chocolate Maker Finally Said Yes to Modern Automation (And What Other Food Manufacturers Can Learn)” by Nicolas Hardy was published on 02/18/2025 by blog.robotiq.com