Understanding the overall cost of palletizing solutions is an important step in the decision making process. This blog provides insights into the factors influencing this cost, including initial investment, ongoing expenses, ROI, intangible benefits, and scalability considerations.
Initial investment
There are many factors to consider with the initial automated palletizing solution investment, so let’s start with the quoting stage.
Budget pricing vs. quoted pricing
Make a clear distinction between estimated (budgetary costs) and specific price quotes. This approach is crucial to ensure a fair and accurate comparison of each alternative. Take note of the vendor’s recommended budget contingency or the extra room they recommend as a precautionary measure to accommodate additional costs.
Essential vs. nice-to-have features
The Robotiq Buyer’s Guide includes a tool to assist in evaluating the needs of the palletizing process and determining the significance of each requirement. Based on these needs, certain solution categories will become apparent as potential candidates. This tool is called the Detailed Specification Sheet and can be downloaded with this link. It is recommended that this tool is used prior to assessing system costs so it can be used as a reference.
Detailed Specification Sheet (from The Automated Palletizing Buyer’s Guide)
Integration
Certain automated palletizing solutions may require more substantial (and perhaps intricate) integration efforts. The level to which a solution aligns with the existing factory processes, layout, and systems is important to understand. Here are questions to ask the vendor to help kick start that discussion:
- Will the chosen platform allow you to automate other stations in your factory or in sister companies?
- How well does the solution accommodate our current factory layout?
- What level of compatibility does the solution have with our existing systems?
- How extensive are the integration efforts?
- Are there any prerequisites or modifications needed in our current processes for successful integration?
- Can you provide examples of successful integrations with similar factory setups?
Customization
If the solution does not cover the essential features required for the palletizing application, there might be additional customization costs. The initial customization costs should be considered, as well as the need for ongoing cost- of-ownership expenses to maintain the system’s relevance and functionality. This includes additional customization expenses over time as the system evolves and remains in operation. Referring to the Detailed Specifications, expenses associated with each customization to incorporate the essential features should be considered.
Vender lock-in
When assessing the initial cost of palletizing solutions, the potential long-term costs and consequences of selecting the vendor must also be considered. Vendor lock-in may have an impact on changes, scalability, and other factors. Considering this in the review of the alternatives can affect the cost of ownership portion of the ROI calculation.
Scalability
Finally, it is important to consider the scalability of a solution and how it might influence the cost of ownership. Here are some questions to consider:
- Does this solution require a larger upfront investment but then reduce the costs of subsequent upgrades?
- Does this solution enable a modest investment and offer the possibility to expand as needed?
- Will it be possible to scale the solution and expand its capacity as the requirements evolve?
- What would be the upgrade costs?
The following table outlines the Initial Investment Considerations for each solution type. These are relative representations between each category to assist with decisions.
Initial Investment Considerations (from The Automated Palletizing Buyer’s Guide)
Operating costs
The operating costs for a robot palletizer can vary significantly depending on several factors:
- Energy costs: Energy costs depend on system efficiency, runtime, and the local electricity rates.
- Maintenance and repairs: Regular maintenance and repairs contribute to operating costs. It is important to understand who is authorized to perform maintenance, proposed service contracts, and how spare parts are purchased. If possible, a current customer of the vendor can provide insights from the user’s standpoint. The proposed maintenance and support packages offered by the supplier should meet the company’s expectations.
- Training costs: The cost of training existing and new employees on the system should be compared. Current customers can provide a clear view of the training experience their team received.
- Programming and software updates: It is important to document software license costs and subscription costs. Equally as important is clarifying the responsibilities for program additions and changes. Can existing employees handle these tasks, or does it involve external individuals?
Unexpected costs are frustrating. Keeping track of all potential expenses increases the likelihood of obtaining a more accurate estimate of the initial investment and operating true costs.
ROI considerations
Now, understanding the initial and ownership costs from the previous chapter, the logical next step is to project the Return on Investment (ROI).
The previous financial information should be supplemented with productivity gains and labor impact information in order to compare with manual palletizing operations.
As a reference, here are a few investment calculations that are used at this step:
ROI formula: (Net Gain from Investment / Initial Investment Cost) x 100
Net gain formula: Savings in costs (labor, downtime, etc.) + Additional revenue from increased productivity.
Quantifying productivity gains:
- Cycle time: Duration to complete a specific task or produce an item.
- Output: Number of units processed per unit of time.
- Scalability: Ability to increase volume with minimal additional cost.
Quantifying impact on labor:
- Labor costs: Current manual labor costs, including wages and benefits.
- Labor efficiency: Productivity and efficiency of manual labor.
- Labor flexibility: Ability to reassign labor for various tasks.
Cost of ownership
Any investment can have risks. It is important to consider them and have a mitigation plan if they happen.
- Identify risks: Potential risks such as technological failures, market changes, or regulatory issues.
- Risk mitigation: Document strategies to mitigate each risk and calculate the potential cost associated with mitigation.
- Include a risk factor in ROI comparison: Look at the factory’s previous, large-scale, cross- functional investment projects. Were they on time and on budget? If not, add that risk factor to the ROI calculation for Centralized and Engineered solutions that are of a similar nature.
Investment risk assessment
These may not be clear numbers, but they are qualitative gains that need to be considered in the decision process.
- Safety: Decrease costs associated with workplace accidents, medical leave, injuries, and near-misses.
- Employee engagement: Evaluate the influence on workforce morale and the increase in employee retention.
- Quality improvement: Calculate the reduction of costs related to errors.
- Market reputation: Estimate the positive impact on the company’s reputation (both with customers and job candidates) for innovation and efficiency.
Conclusion
Understanding the cost of palletizing solutions is crucial for informed decision-making. This blog has shed light on various factors influencing costs, such as initial investment, integration, customization, vendor lock-in, and scalability. It has emphasized the importance of distinguishing between budgetary estimates and specific price quotes, as well as considering long-term operating expenses and ROI calculations. Moreover, the discussion on intangible benefits highlights the broader impacts beyond financial metrics, including safety improvements, employee engagement, quality enhancement, and market reputation.
By carefully analyzing these financial considerations, businesses can make strategic investments in palletizing solutions that align with their operational goals and deliver long-term value.
Download the Robotiq Automated Palletizing Buyer’s Guide or additional tools, helpful tips, and tangible resources.
Ready to start? Talk with one of our palletizing experts.
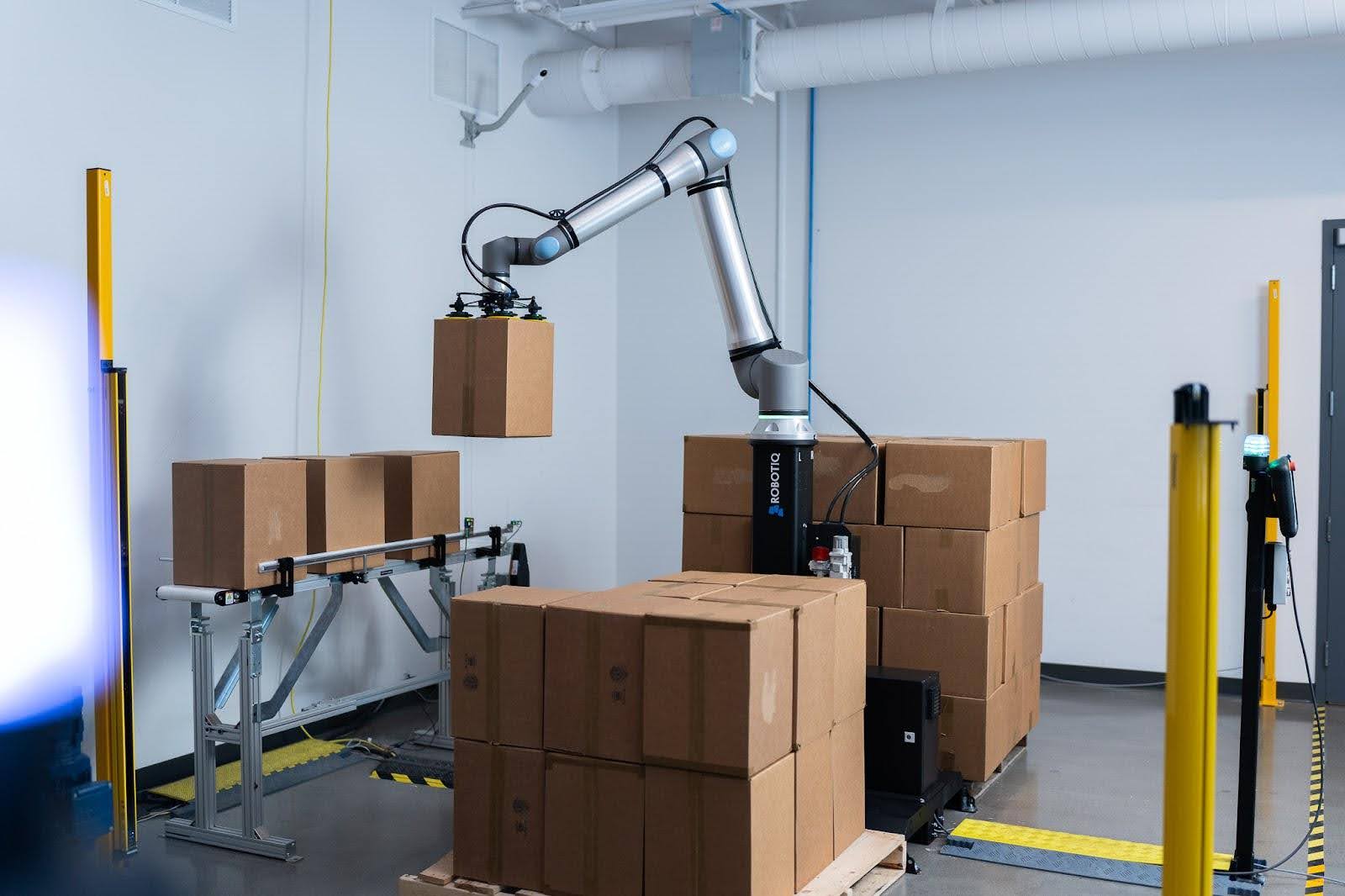
The post “Financial Considerations: The Cost of Palletizing Solutions” by [email protected] (Nicolas Lauzier) was published on 05/20/2024 by blog.robotiq.com