The workforce in manufacturing is aging rapidly. Baby Boomers, who make up a significant portion of the industrial labor force, are retiring in droves. More than 25% of the manufacturing workforce in major economies is over 55 years old.
With governments raising retirement ages to align with increasing life expectancy, businesses must adapt workplaces ergonomically to accommodate older workers. Compounding this demographic shift is a tight labor market, where shortages are expected to reach millions globally by 2030.
Manufacturers can no longer rely on abundant labor to sustain growth. The consequences of ignoring these trends are severe—reduced production capacity, a widening knowledge gap as experienced workers retire, and significant health and safety risks for an aging workforce. Solutions must address these challenges while ensuring operational continuity and growth.
*Photo by Ahsanization ッ on Unsplash
Aging Workforce Challenges
1. Rising Labor Costs
Labor costs in manufacturing have risen significantly in recent years, driven by inflation and the need to attract scarce talent. Between 2021 and 2023, these costs increased by nearly 10%, with some regions experiencing hikes as high as 15%. Rising wages, overtime pay, and reliance on temporary workers further strain manufacturers’ budgets.
Automation provides a compelling solution to manage escalating labor costs. Key benefits include:
- Streamlined Operations: Collaborative robots (cobots) and automated systems reduce reliance on manual labor while improving productivity.
- Cost Savings: Automated processes minimize waste and inefficiencies, delivering measurable cost savings and consistent ROI.
- Scalability: Automation enables manufacturers to scale operations without proportional increases in labor costs.
2. Addressing High Turnover Rates
Employee turnover in manufacturing is alarmingly high, with rates reaching 20-22% in some regions. This disrupts workflows, erodes team cohesion, and leads to significant costs associated with recruiting, onboarding, and training. High turnover also impacts customer satisfaction, as continuity in the workforce is essential for maintaining quality and trust.
To combat these challenges, manufacturers can:
- Invest in Automation: Automated systems reduce dependence on a constantly changing workforce by taking over repetitive tasks, ensuring stable productivity levels.
- Enhance Engagement: Providing meaningful work, contemporary tools, and career development opportunities fosters a positive workplace culture and reduces turnover.
- Offer Competitive Compensation: Competitive wages and benefits, along with flexible work options, make it harder for employees to seek alternatives.
- Focus on Training: Upskilling and reskilling programs demonstrate commitment to employees’ growth, boosting retention and aligning the workforce with evolving industry needs.
- Improve Work-Life Balance: Flexible hours, paid time off, and ergonomic enhancements attract younger generations who value well-being and flexibility.
3. Shifting Workforce Preferences
Younger generations, including millennials and Gen Z, show a marked reluctance to take on traditional manufacturing roles. Only 29% express willingness to engage in “3D” jobs—those considered dull, dirty, or dangerous. Instead, they prioritize meaningful work, flexibility, and work-life balance.
For manufacturers to attract and retain younger talent, it is crucial to:
- Redesign Jobs: Create roles that offer purpose, flexibility, and growth opportunities.
- Modernize Workplaces: Introduce advanced tools and technologies to appeal to tech-savvy younger workers.
- Prioritize Safety: Enhance job safety and ergonomics to make traditional roles more attractive.
Automation can bridge the gap by eliminating undesirable tasks, allowing younger workers to focus on higher-value activities. Companies that embrace modern tools and create supportive work environments are better positioned to attract top talent.
The Role of Automation
Automation emerges as a critical strategy to mitigate the impact of an aging workforce. By automating repetitive and physically demanding tasks, manufacturers can:
- Fill Labor Gaps: Automated systems ensure production continuity without full reliance on human labor, alleviating the strain of labor shortages.
- Enhance Ergonomics: Automation reduces the physical strain on older workers, enabling them to focus on less taxing and more complex tasks.
- Preserve Knowledge: Automation allows manufacturers to streamline operations while facilitating knowledge transfer from retiring employees to new hires through upskilling initiatives.
In addition, promoting ergonomic workplace designs—such as improved workstations and reduced manual handling—ensures the safety and productivity of an aging workforce.
Overcoming Barriers to Automation
Despite its clear advantages, several barriers hinder automation adoption in manufacturing:
- Lack of Technical Skills: A shortage of skilled IT and engineering professionals creates challenges in implementing and managing automated systems.
- Reliance on External Experts: Over-dependence on systems integrators can slow adaptation and increase costs.
- Integration Challenges: Complex and costly integration processes deter manufacturers from adopting new solutions.
- Financial Concerns: High upfront costs and fears of scope creep often create hesitation, particularly for small-to-medium-sized manufacturers.
- Workplace Culture Resistance: Employees may fear job displacement or struggle to adapt to new technologies.
- Fragmented Processes: Manufacturers with bespoke production workflows may perceive automation as incompatible with their operations.
To overcome these barriers, manufacturers should:
- Choose Flexible Solutions: Invest in modular, scalable automation technologies that can adapt to changing production needs.
- Minimize Labor Dependency: Focus on systems that reduce reliance on both manual labor and highly specialized technical skills.
- Avoid Vendor Lock-in: Select interoperable systems that allow flexibility in vendor choice and upgrades.
- Evaluate ROI Carefully: Opt for solutions with clear implementation processes and short ROI timelines to ensure measurable value.
- Promote Change Management: Foster a workplace culture that embraces innovation through transparent communication and employee involvement.
Automation Strategies: End-to-End vs. Task-Based
Manufacturers can approach automation through two primary strategies:
- End-to-End Automation: Designed to integrate multiple systems and processes seamlessly, this approach is ideal for managing complex workflows. While it requires significant investment and planning, it delivers comprehensive operational efficiency.
- Task-Based Automation: Focuses on automating specific repetitive tasks, making it easier and faster to implement. This strategy provides flexibility and quick returns, particularly suitable for environments with frequent workflow changes.
The choice between these strategies depends on factors such as the complexity of factory processes, scalability requirements, investment capacity, and workplace culture. In many cases, a hybrid approach—starting with Task-Based Automation and transitioning to End-to-End solutions—proves effective.
Why Automation is Now a Necessity
Manufacturers face an era where customers and shareholders accept no excuses for inefficiency or inaction. Automation has transitioned from a competitive advantage to a critical necessity. Key reasons include:
- Health & Safety: Automation reduces workplace injuries by eliminating hazardous manual tasks.
- Productivity: Automated systems improve efficiency, consistency, and throughput, often delivering ROI within a year.
- Adaptability: Automation ensures continuity and scalability, preparing businesses to handle labor shortages, supply chain disruptions, and evolving market demands.
- Employee Engagement: By automating monotonous tasks, employees can focus on creative, value-driven activities that enhance job satisfaction.
According to Deloitte, 86% of manufacturing executives view smart factory solutions as essential for competitiveness in the next five years. Economist Alan Beaulieu emphasizes the urgency of investing in automation now to secure a competitive edge before economic conditions improve.
Conclusion
The structural challenges facing manufacturers—aging workforces, rising labor costs, high turnover, and shifting workforce preferences—demand strategic action. Automation offers a viable, scalable solution to address these issues while driving productivity, efficiency, and employee engagement. By overcoming barriers to adoption and strategically implementing automation technologies, manufacturers can secure their long-term viability in an evolving industrial landscape.
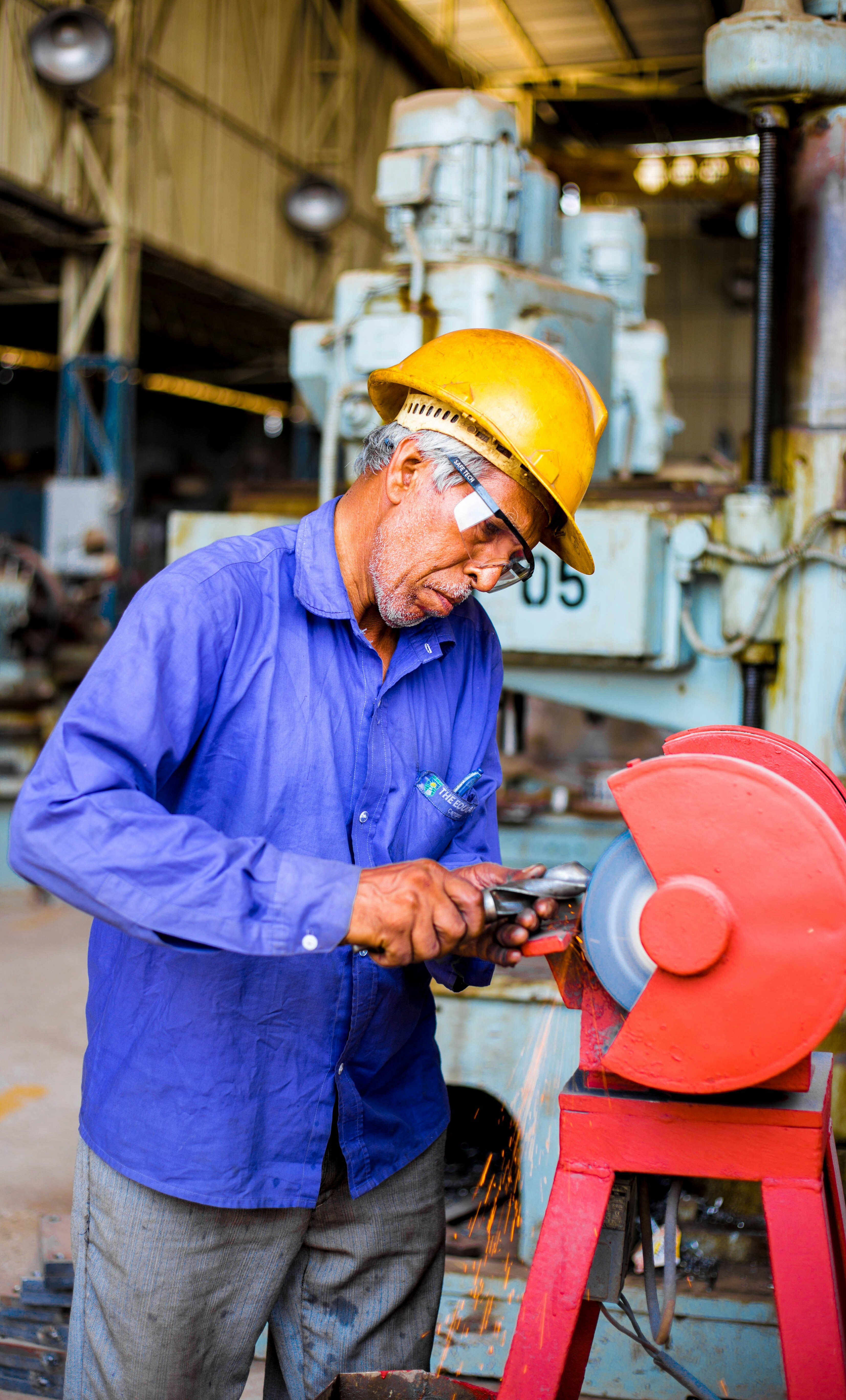
The post “Aging Workforce Challenges for Businesses (and Solutions)” by [email protected] (Samuel Bouchard) was published on 01/29/2025 by blog.robotiq.com